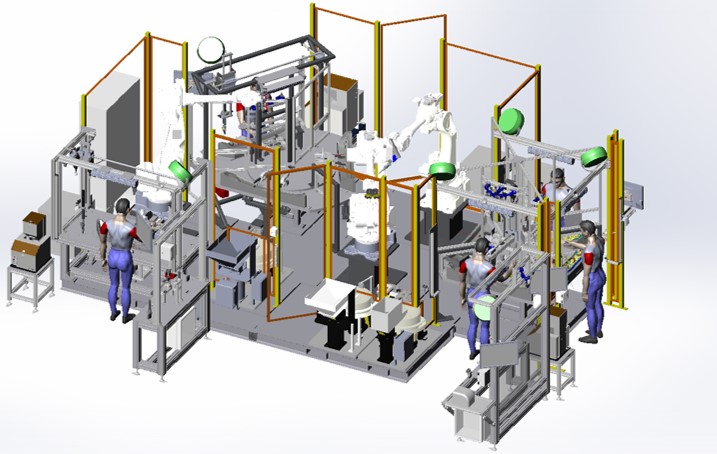
A Tier 1 automotive supplier engaged with Mesa Technologies to design and build a semi-automatic assembly cell.
The load operator will load an upper and lower housing to a fixture and affix a customer emblem. A 6-axis robot will transfer the components to a dial plate/indexer station. The dial plate/indexer rotates and advances the part to Operator #2. This operator uses a handheld automated screwdriver to drive several screws, joining the upper and lower housing The indexer cycles again and transfer the workpiece to a clip assembly station where 6-axis robots install retainer clips to the sub-assembly. After the clips are assembled, a 6-axis robot transfers the sub-assembly to a second dial plate/indexer
The indexer cycles and transfers the workpiece to Operator #3, who installs additional hardware and brackets to the sub-assembly. The indexer cycles again to move the part to Operator #4, who installs a back up camera to the sub-assembly. The indexer then moves the workpiece to Operator #5. This operator removes the completed part from the machine and places on a test fixture. This fixture test the operation of the back up camera and is manually inspected for retainer clip presence.
After inspection, good parts are packed for shipment to their customer, reject parts are collected for rework and/or disposal.