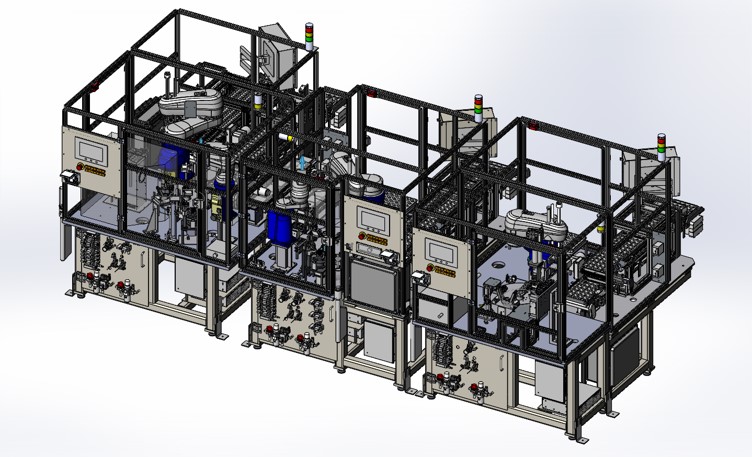
A Tier 1 automotive supplier engaged with Mesa Technologies to design and build a fully automatic assembly cell.
Our customer had an existing production line that had been in production for approximately 20 years. The product line was forecast to continue for an additional 10 years. The previous machines had several mechanical and electrical components that had become obsolete and were becoming extremely difficult to replace. The machine ran multiple shifts and could not be taken out of service for refurbishment. The previous machines also required operators to load and unload the workpieces.
Mesa worked with our customers to understand and reproduce the same assembly processes as the previous machines. We modified the design to eliminate the need for the load/unload operator. This allowed our customer to largely justify the capital cost of the new equipment through headcount reduction
- M/C #1 – Housings are supplied from the back of the machine on trays (same as previous). A robot removes a workpiece from a tray and places it on a dial plate/indexer. A laser mark was added for traceability. Components are added to the assembly on the dial plate. The sub-assembly workpiece is unloaded from the dial plate and placed onto an “in-process tray” for curing.
- M/C #2 – The process is repeated, and additional components are added to the sub-assembly.
- M/C #3—The sub-assembly is loaded into the machine on “in-process trays.” A robot transfers the workpiece to a dial plate. The workpiece undergoes a leak test. If no leaks are detected, a protective epoxy is dispensed to complete the assembly. The completed workpiece is then reloaded to an in-process tray and transferred out of the machine.
Fully Automatic Assembly Cell Read More »