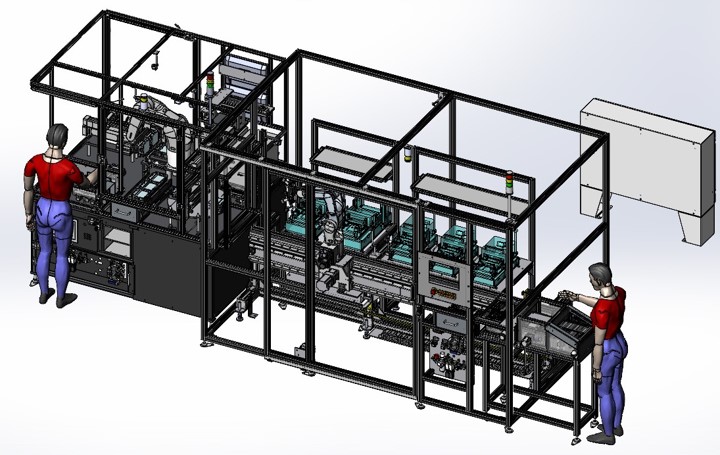
A Tier 1 automotive supplier engaged with Mesa Technologies to design and build an automated assembly / testing machine.
Two components are loaded into a locating fixture by an operator. Cycle start is initiated. A 6-axis robot transfers the two components to an assembly station. The two workpieces are pre-assembled by the robot. A IAI servo press is then cycled to complete the press fit assembly. The station measures and verifies that force required to assemble the components is within specification. The workpiece is then checked by a Keyence Vision system to verify the two components were assembled correctly. Reject parts are placed in a reject drawer for an operator to retrieve and disposition. Good parts are transferred to a nest to be picked by the next machine.
The following machine consists of 5 electrical test stations. A 7-axis robot picks an assembled workpiece from the previous machine. The robot waits for one of the five testers to finish testing of a previous part. The robot then moves to that tester, unloads the workpiece that has just completed testing and immediately reloads the empty tester with the workpiece from the assembly machine. Workpieces that fail the electrical testing are transferred to a reject drawer near the unload operator for retrieval. Workpieces that pass the electrical testing are transferred to the unload operator at the end of the testing machine